Welding is always a tricky method. A tiny mistake can bring severe consequences. Do you know that different types of welding methods matter in this case? Safety, welding quality, and efficiency all differ from one method to another. “Laser welding vs MIG welding” is a crucial topic.
Why is it crucial to discuss laser welding VS MIG welding? Both methods are widely available worldwide. Laser beam welding is safe, reliable, and perfect for welding average sheet metal thicknesses. On the other hand, MIG welding performs better for thicker metals.
Therefore, the correct method generally depends on the type of specific project application. Overall, laser beam welding is widely used in the modern world. You will know “why” in the following few sections.
What is MIG Welding?
MIG stands for Metal Inert Gas, also known as Gas Metal Arc Welding (GMAW). It is also known as a wire welding method.
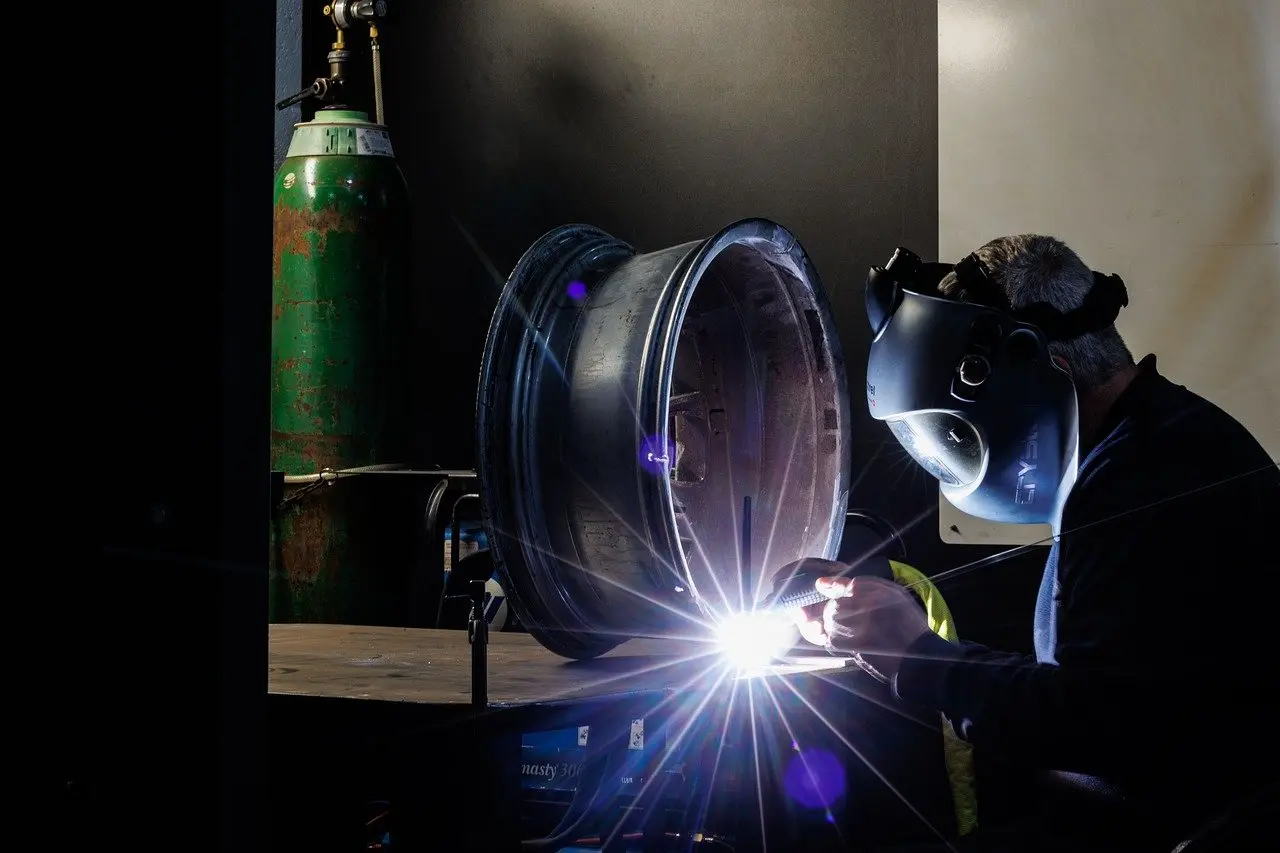
Most people may be confused about the concepts of TIG and MIG. Both are arc welding methods, but they have some differences. In MIG welding, the wire usually acts as both electrode and filler. The wire itself melts and acts as an adhesive when joining two metal parts.
However, in TIG, the tungsten tip generally heats the metal surfaces and allows them to join together. That is why TIG welding is called the non-consumable electrode method.
Pros
- MIG welding is excellent for welding thicker metals. This method is versatile for various thicknesses of metals.
- MIG welding is cheaper to buy the first time. Although, in the long run, it needs consumables (wire and inert gases), which may increase the total TOC.
Cons
- MIG welding needs expertise. Beginners can make several mistakes, which create safety concerns.
- MIG welding is less accurate than laser welding. You know, it needs manual labor.
- This welding method is slower than laser welding. Thus, its productivity is relatively lower.
- This welding method creates more HAZ (Heat Affected Zones).
- MIG welding is not suitable for thin metal parts.
- MIG welding is more prone to porosity, spatter, and inclusions.
- This welding method requires consumable materials, increasing the machine’s overall cost.
What is Laser Welding?
Laser welding is now a trendy method. You will also prefer this welding method for your job. Why? Because laser welding can significantly mitigate the cons of MIG welding. This method is fast, accurate, and versatile. That’s all we need in modern metal parts and equipment.
If you buy a handheld laser welding machine, you will find two main parts: a laser generator and a welding torch. Now open the laser generator cabinet. What do you see? You will find a wire feeder, and on top of that, there’s a laser source device. You will find a welding torch outside the cabinet connected to both devices.

During laser welding, the high-power laser beam projects on the metal surface. It increases the heat on that specific area, and with the help of filler, it joins two separate metal parts. The process is simple yet effective. All you need is some basic knowledge about laser welding.
Pros
- Laser welding is high-speed and accurate. This machine uses a highly focused laser beam that projects only on the area to be welded.
- Laser welding also produces fewer heat-affected zones. This means that your metal parts can preserve the structural integrity after the welding.
- This method may be more expensive initially but will ultimately lower operating costs.
- Laser welding is super easy to handle. Even with less expertise, you can laser weld on many metals.
Cons
- Laser welding may not be suitable for thicker metals.
- Laser welding initially has a high cost compared to MIG welding.
Laser Welding VS MIG Welding: Which is Better?
We have learned enough about laser welding and MIG welding. This section will compare them to find the best solution, considering a few factors. Check out the following table for a quick overview of their primary differences.
Factors | Laser Welding | MIG Welding |
Precision | High Precision | Less Precision |
Accuracy | Very Accurate | Less Accurate |
Speed | Very Fast | Slower than Laser welding |
HAZ | Very narrow, minimal distortion | broader, more risk of thermal distortion |
Versatility | Suitable for thin to thicker materials but struggles with very thick metals | Versatile but struggles with thin metals |
Weld Quality | High-quality, fewer defects | Good quality but more prone to defects |
Expertise | Less skill needed | Higher skill required |
Initial Cost | High | Low |
Operating Cost | Low | High |
Laser Welding VS MIG Welding: Ease of Use
Laser welding has both manual and automatic features. Once installed, it requires little skill to operate. Don’t worry about the installation process. Our customer service team is always here to assist you. If it is for automated welding, you may need some programming skills. Still, don’t worry! We have all the solutions for you.
MIG welding, on the other hand, is easier to learn initially but doesn’t need programming. You know it’s fully manual. However, you will need expertise in how to weld different metals. Note that MIG welding is prone to defects. Therefore, expertise is essential here.
Laser Welding VS MIG Welding: Precision & Accuracy
Laser welding comes first when you look at how accurate each welding method is. If you observe the working mechanism of laser welding, you will know why it is so precise. Well, laser welding uses highly focused laser beams. This tiny beam only hits the area that needs to be welded. As a result, you can get exact welding. This is why people often prefer laser welding over MIG welding.
On the other hand, MIG welding is less precise than laser welding. It is generally not suitable for intricate welding. It also produces more distortion. However, you can only consider MIG for a general-purpose job.
Laser Welding VS MIG Welding: Speed & Efficiency
Laser welding is much faster than MIG welding. As you know, laser welding is precise and accurate, so it doesn’t need any post-welding jobs. Because of this, laser welding proves to be highly efficient. As a result, it is excellent for high-volume production.
On the other hand, MIG welding is usually slower than laser welding. Unlike laser welding, it needs post-welding jobs. Because of this, MIG welding is not as efficient as laser welding. As a result, MIG is not suitable for mass production.
However, if you buy a desktop laser welding machine, you can get even faster results. These machines are fully automated so that you can ensure consistent welding quality in mass production.
Laser Welding VS MIG Welding: HAZ & Distortion
HAZ and distortions are two crucial factors you can also consider. Laser welding creates a very narrow HAZ. Because of this, you get minimal thermal distortion. MIG welding, on the other hand, makes a bigger HAZ, which can lead to more distortion. This generally affects the integrity and appearance of the welded material.
As you know, laser welding offers superior control over heat and distortion. Thus, it is often the best way to weld delicate components. However, MIG welding is technically not suitable for these jobs.
Laser Welding VS MIG Welding: Material Versatility
Laser welding offers excellent versatility. It can work with almost all types and thicknesses of metal. Stainless steel (SS), carbon steel (CS), aluminum, and titanium are popular metals in this case. However, note that you may need higher laser powers for thicker metals. You can typically get laser powers from 500W to 3000W for a handheld laser welder. Check out the following table to get a general idea.
Metal | 500W | 1000W | 1500W | 2000W | 3000W |
Aluminum | 2mm | 3mm | 4mm | 5mm | 8mm |
Stainless Steel | 3mm | 5mm | 7mm | 8mm | 10mm |
Carbon Steel | 6mm | 10mm | 12mm | 16mm | 20mm |
Copper Plate | 2mm | 3mm | 4mm | 5mm | 8mm |
MIG welding is also versatile. However, it may get messy when working with thin materials. MIG welding is also practical for steel, titanium, and aluminum.
Laser Welding VS MIG Welding: Cost
When you first buy a laser welding machine, it will be expensive. However, it can be a cost-effective solution for your project in the long run. As you know, laser welding produces precise welding. Thus, it doesn’t need any post-welding tasks. In addition, laser welding needs less maintenance than MIG welding. It generally reduces a significant amount of operating costs.
On the other hand, MIG welding may be more affordable when purchased. However, in the long run, the consumables and maintenance increase the overall operating costs.
Laser Welding VS MIG Welding: Safety
If you think of safety, laser welding is much safer than MIG. Laser welding produces less dust and less fumes, which makes it safer for people to breathe. It means being less close to heat and molten metal. Burns are less likely to happen because the laser beam is directed. Automation improves safety even more by lowering the need for operators.
Is Laser Welding Better Than MIG?
If you are dealing with thin metals or delicate components, laser welding is definitely the best choice. As you know, laser welding is fast and accurate. Most importantly, it produces minimal distortion.
On the other hand, laser welding should be chosen for metals with thicknesses less than 20mm. It is better than MIG welding. However, if the thickness is more than 20mm, it is better to go for MIG welding.
Laser welding is the best option, considering the weld quality and accuracy. In contrast, MIG welding is suitable for general-purpose and cost-effective applications.
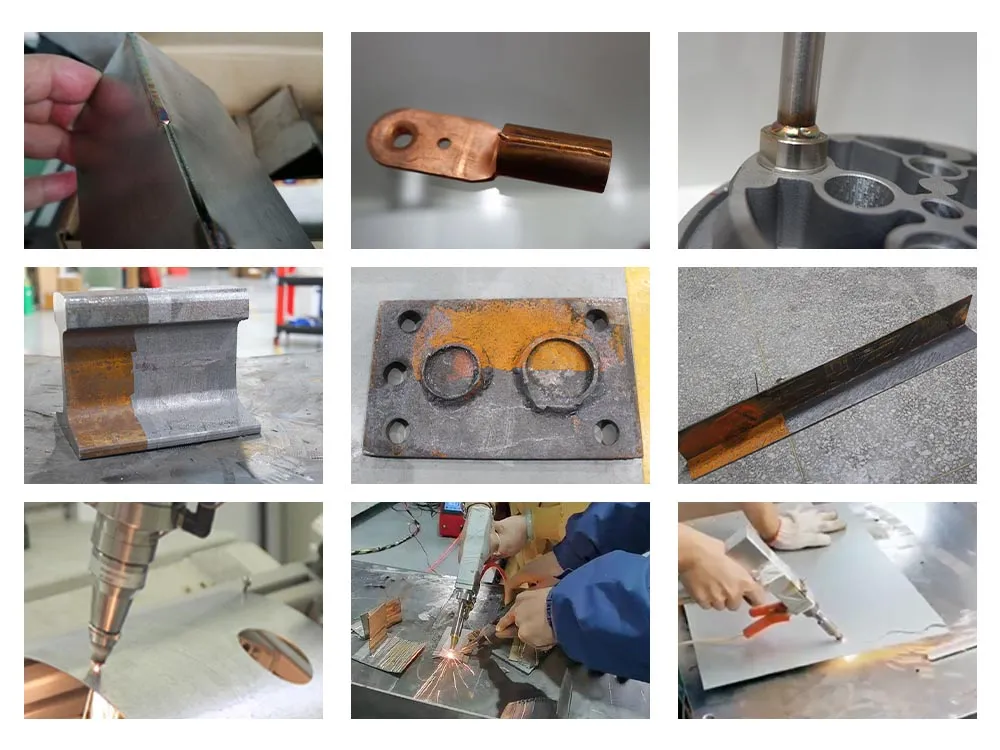
Contact Us Today
If you have questions, feel free to contact us. Our team is ready to assist you. We offer high-quality laser welding devices (both handheld and desktop). Reach out to discuss your project. Let’s make your welding project a success.